顧客満足とコストを最適化する「受注生産」と「見込み生産」のバランスとは
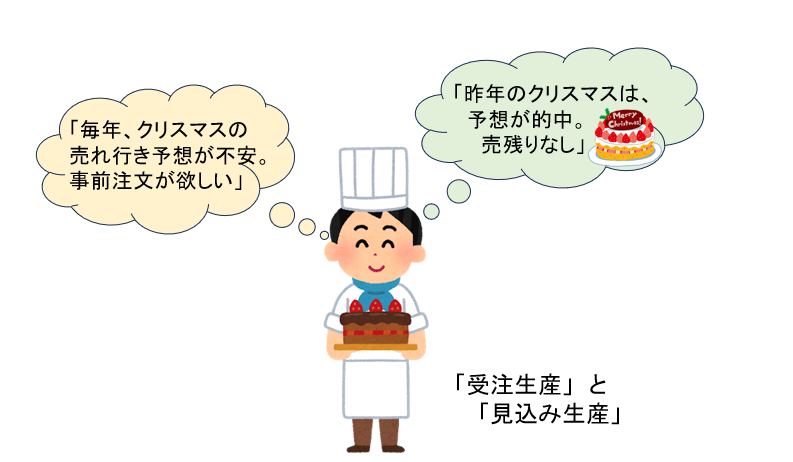
顧客満足とコストを最適化する「受注生産」と「見込み生産」のバランスとは
顧客満足とコストを最適化する「受注生産」と「見込み生産」のバランスとは
「お客様の好みに合わせたパソコンを素早く提供」
「お好きな色、仕様の車を提供」
こんな謳い文句で商品を売っている会社があります。注文を受けてから生産する「受注生産」のように聞こえます。しかし、実際には、あらかじめ用意された選択肢の中から顧客が好みの要素(部品や機能)を選んでもらい、メーカーにて組み上げて製品となります。この方法では、比較的短期間でお客様の満足するオリジナリティ性のある製品が提供できます。選択肢となる部品や色(塗料)などの構成要素は、「見込み生産」で前もって作られ在庫されています。もしも、構成要素である部品、塗料などをお客様の注文があってから製造(調達)するとしたら、とんでもない時間とコストが掛かります。
生産には、大きく分けて「注文生産」(Make to Order)と「見込み生産」(Make to Stock)とがあります。「注文生産」とは、注文を受けてから生産を開始する方法であり、「見込み生産」とは、需要を予測して注文前に生産する方法です。
注文生産では、受注に基づく生産のため製品在庫は最小限ですみます。ところが、注文から顧客に届くまでのリードタイムが長くなる、まとめ生産が出来ずコスト高になるなどのデメリットがあります。一方、見込み生産では、リードタイムが短くなる半面、製品在庫コストが増えたり、売れ残りや売りたい商品が不足したりするリスクがあるというデメリットがあります。
一般的には、高価値かつカスタマイズ性が高い製品(例:航空機、特殊機械、プラントなど)は、「注文生産」が行われ、大量消費される標準製品 (例:食品、日用品など)は、「見込み生産」が行われています。
しかし、実際に市場で販売されている製品は、注文生産と見込み生産を組み合わせていることが主流です。オリジナリティ性の高い「注文生産」と称しても、冒頭に挙げたパソコンや車のように、見込み生産で作った半製品や部品を使い、注文生産の欠点である長いリードタイムやコスト高などのデメリットを小さくして、注文生産のメリットであるオリジナリティ性を上げ、結果として顧客の満足度を上げる工夫がされています。
「注文生産」や「見込み生産」を生産管理という視点からみると、
原材料や部品に対して、いつ顧客の注文(オーダー)と結び付けるか
ということです。この作業を業界によっては、「紐付け」と呼んでいます。(鉄鋼業界など)原材料の段階でオーダーと結びつければ、完全な「注文生産」であり、製品になってからオーダーが付くのが「見込み生産」ということになります。
生産工程のどこでオーダーと結び付けるかは、産業や各企業の考え方(戦略)で変ります。
例えば、クリスマスケーキでは、「見込み生産」で店頭に並べる店もあれば、何か月も前から注文を受付けた「注文生産」の店もあります。また、ベースのケーキを用意して、店頭でお客様の注文でデコレーションをする店もあります。
車の修理は、100%「注文生産」です。しかし、修理の部品をあらかじめ用意していれば、「見込み生産」の要素が入ってきます。
「受注生産」と「見込み生産」の持つメリット、デメリットのバランスをどう保つかは、販売戦略や生産管理を考える上で重要なポイントになります。個々の企業(部門)の生産性、コスト、リスクを決めるのは、このバランスです。更に企業間を含めたサプライチェーンを考えても、「受注生産」と「見込み生産」のバランスは、社会のコストやリスク管理の上で重要です。
この記事では、「注文生産」と「見込み生産」のバランスを保っている例をいくつか紹介します。
例1 商社が、「ジャスト・イン・タイム」を実現している?
原材料や部品を調達して生産している会社、小売りをしている会社の立場からすれば、欲しい品質、欲しい量の原材料や部品、製品が注文したのち速やかに入ることが望ましい姿です。言い替えると使いたい時や売りたい時、ギリギリまで発注せず、発注したらすぐに商品を手に入れるのが理想です。この代表は、自動車会社などで採用されている「ジャスト・イン・タイム」と呼ばれる方式です。一方、原材料や部品の生産者からみれば、この要求に対応するのは容易ではありません。注文量に応じて生産すれば、製品ロットが小さくなって効率が悪い、即納に対応しようとすると製品在庫が増えるといった問題があるからです。
それでも、トヨタなどの自動車メーカーでは、ジャスト・イン・タイムという生産方式を採用し、トヨタの繁栄を支えてきました。そこで、重要な役目を果たしてきたのが、商社(問屋)です。以下、鉄鋼製品を例にして、鉄鋼会社から自動車メーカーに鋼材が供給されるプロセスをご紹介します。
1)需要予測と発注
商社は自動車メーカーの生産スケジュールに基づいて、必要な鋼材の種類や量を予測して、数か月前に鋼材を鉄鋼メーカーに発注します。
2)在庫管理と2次加工
商社は鉄鋼メーカーから必要な鋼材を調達し、必要によっては2次加工(鋼材の切断、プレス加工、表面処理など)を加工メーカーと連携して行い製品在庫とします。
3)「ジャスト・イン・タイム」での納入
商社は、自動車メーカーの指示に合わせて、鉄鋼製品を納入します。(製品は、鉄鋼会社の倉庫、商社の管理する倉庫、2次加工業者の倉庫等々から)
これらの過程で、鉄鋼会社は、最終顧客である自動車メーカーに対して、「見込み生産」をしているのですが、商社に対しては、「受注生産」を行っていることになります。自動車会社から見ると、ジャスト・イン・タイムに製品が届く、あたかも「見込み生産品」を調達しているような感覚です。この間の矛盾、例えば自動車の生産が減少して、鋼材の在庫が膨らむなどのリスクを商社が担っています。
例2 食品販売で、中間業者(卸業者)を省くとは、「売れ残り」リスクの再配分
食料品などスーパーマーケットで売られているような一般消費品は、店頭に並べて売られています。消費者からみると「見込み生産」で作られた商品を手にし、購入していることになります。食料品を生産している食品加工メーカーは、中間業者(卸御者や問屋)の注文に対して生産している「受注生産」です。中間業者は、小売り(スーパーマーケットや各商店)に商品を提供し、小売りは消費者に提供します。この過程で、生産量と需要との差から生まれる、「売れ残り」や「品不足」のリスクを中間業者や小売業者が分担していることになります。
最近の流れである製造者による通販、中間業者をぬいて小売りと食品メーカーとの直接取引は、中間業者に払われるコスト(マージン)を省く代わりに、食品メーカーや小売業者が売れ残りや品不足のリスクを取るということです。
例3 修理は、「注文生産」の典型。これを「見込み生産」の部品が支える
家電や車の修理は、「注文生産」の典型です。壊れた家電や車を修理業者に持ち込んで、素早く直すことを求められます。スマホや家電製品であれば、修理業者は、よくある故障を想定してあらかじめ用意してある部品を使い直します。部品が小さく安価であれば、在庫を持つコストが問題とならず、この方法が成立します。
車の場合では、修理用の部品点数が多く、部品には大きなものもあって修理業者が保管するには制約があります。その結果、修理の依頼がある度に修理用部品をメーカーから取り寄せて修理ということになります。部品があればいいのですが、車の生産が一定期間を過ぎた部品(トヨタでは、車の生産終了から10年程度)やレアな車種では、手に入らないこともあります。すると部品から作ることになり、修理に長い期間を要することになります。
部品調達で有力なのが、ネットワーク情報の活用です。私は、依然米国で車を損傷させたことがあります。オハイオ州の田舎道でタイヤがバーストして側溝に落ち、走行できなくなって3A(日本のJAFのような団体)に助けを求めました。壊れた車を、近くのガソリンスタンドに運び、修理を依頼しました。車は、ホイールを含めたタイヤとフェンダーがダメになっており、修理に時間がかかると思っていたのですが、なんと2日後には、元通りになって戻ってきました。修理用の部品は、全て中古品で取り換えてコストも抑えてありました。中古パーツのネット市場があり、全米からすぐに調達できるとのこと。ガソリンスタンドのおやじいわく、
「ネットで見つからなければ、スクラップ車の置き場にいって調達する」
とのこと。背景として、日本にはない分厚い中古パーツストックが米国にはあります。
米国では、日本に比べて中古車価格が高いこともあって、修理用の中古部品の流通量が圧倒的に多く、かつネット情報が充実していて、田舎町の小さな業者でも、短期間で修理をしてくれます。
「見込み生産」による在庫リスクを、ネットワークを活用することで分散させているという実例です。
まとめ
「受注生産」と「見込み生産」の持つメリット、デメリットのバランスをどう保つかは、販売戦略や生産管理を考える上で重要なポイントになります。個々の企業(部門)の生産性、コスト、リスクを決めるのは、このバランスです。更に企業間を含めたサプライチェーンを考えても、「受注生産」と「見込み生産」のバランスは、社会のコストやリスク管理の上で重要。
参考記事:日本の製造業の生産性向上には、経営の4つの課題解決が必要